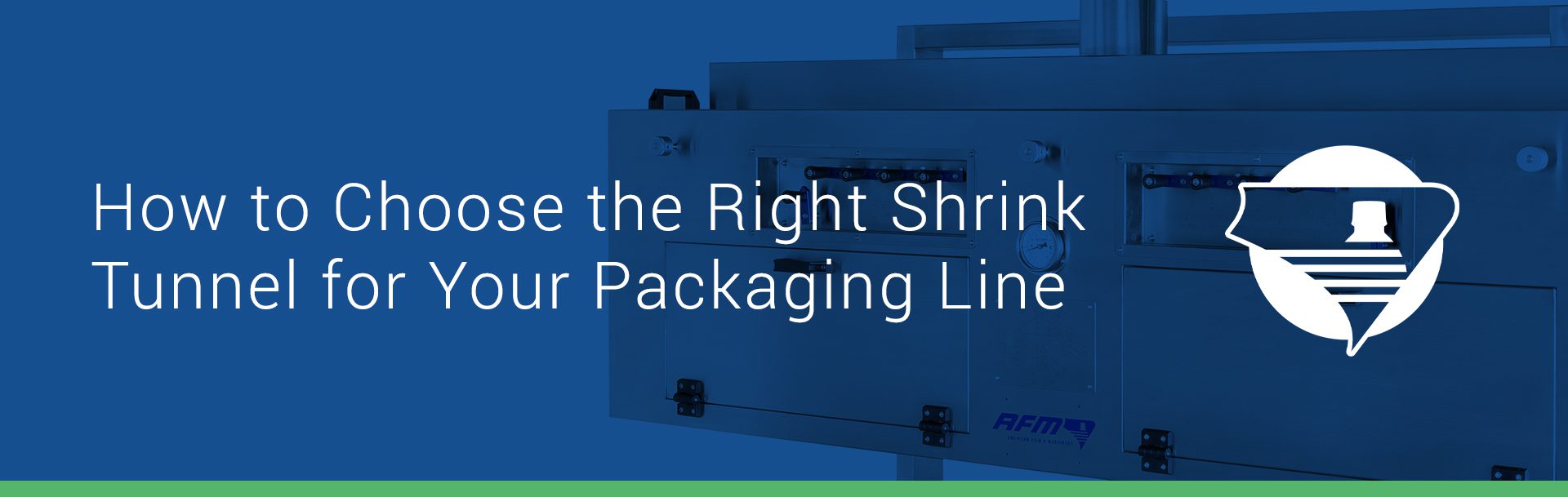
How to Choose the Right Shrink Tunnel for Your Packaging Line
In the world of packaging, a perfect label is more than just decoration — it’s a reflection of your brand’s quality and professionalism. For businesses that rely on shrink sleeve labeling, the shrink tunnel plays a crucial role in achieving that flawless, form-fitting finish.
But choosing the right shrink tunnel isn’t always straightforward. With a variety of tunnel types, heating technologies, and configurations available, how do you determine which one is right for your packaging line?
This article breaks it all down — helping you choose the shrink tunnel that matches your product, production demands, and budget.
What Is a Shrink Tunnel — and Why Does It Matter?
A shrink tunnel is a heated chamber designed to apply consistent heat to shrink sleeve labels or shrink-packaging film around a product. As containers pass through the tunnel on a conveyor, heat causes the label to conform tightly to the shape of the container — creating a seamless, professional look.
Shrink tunnels are essential in industries like food and beverage, personal care, household products, and pharmaceuticals where product presentation, tamper evidence, and durability matter.
Key Factors to Consider When Choosing a Shrink
Tunnel
- Product Shape and Size
- Uniform Products: Simple tunnels may suffice for cans, bottles, or jars.
- Irregular Shapes: Steam or customizable tunnels handle contours, curves, and specialty shapes better
- Production Speed Requirements
- Low to Medium Speeds: Electric hot air tunnels are usually sufficient.
- High Speeds: Steam or high-capacity infrared tunnels provide faster throughput without sacrificing quality
- Film Type Compatibility
- Different shrink films react to heat in unique ways:
- PVC: Shrinks at lower temperatures.
- PETG: Durable, highly conformable; requires precise, even heat.
- OPS: Eco-friendlier but shrinks less aggressively.
- PLA: Biodegradable but sensitive to overheating.
- Matching your film to the tunnel type is critical for avoiding wrinkles, bubbles, or tears.
- Different shrink films react to heat in unique ways:
- Tunnel Type: Which Heat Source?
- 🔥 Hot Air or Electric Tunnels
- Best for basic applications or lower-volume lines.
- Simple, compact, and affordable.
- May struggle with complex shapes.
- 💡 Radiant or Infrared Tunnels
- Targeted, efficient heating.
- Good for high-speed lines or products requiring precision.
- 💧 Steam Tunnels
- Ideal for complex, contoured, or heavy-duty applications.
- Delivers even heat distribution.
- Requires water supply and drainage.
- 🔥 Hot Air or Electric Tunnels
- Energy Efficiency
- Check energy consumption based on tunnel type.
- Steam tends to use more water but less electricity.
- Infrared and electric tunnels may save on utilities depending on your facility
setup
- Facility Space and Layout
- Footprint matters. Modular and compact tunnels are available for tight spaces.
- Conveyor integration is critical — ensure compatibility with your upstream and
downstream equipment.
- Ease of Maintenance and Durability
- Look for heavy-duty components built for continuous use.
- Prioritize tunnels with accessible parts, simple cleaning processes, and robust
warranties
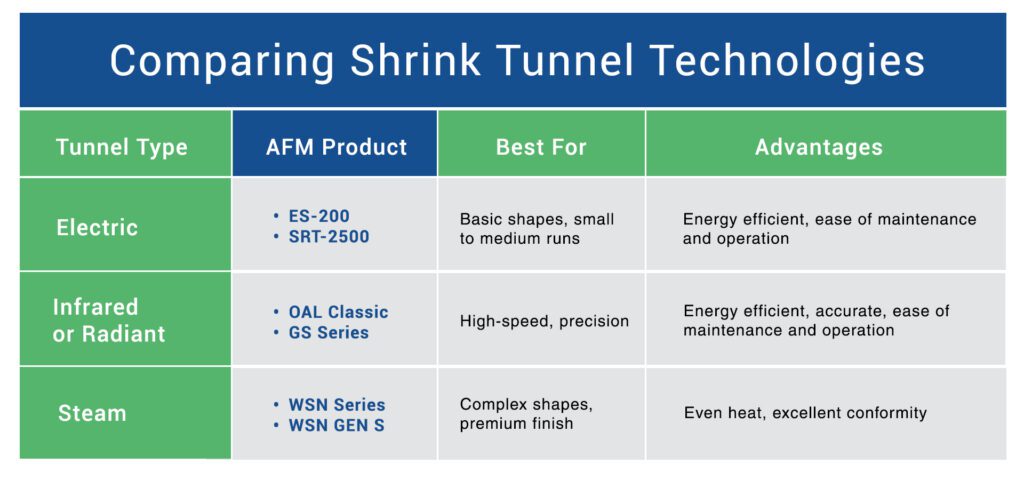
Common Mistakes to Avoid
- 🚫 Choosing the Wrong Size: Undersized tunnels cause poor shrink; oversized wastes energy and space.
- 🚫 Ignoring Film Specs: Using the wrong tunnel for your shrink film leads to poor label performance.
- 🚫 Overlooking Airflow and Heat Zones: Inadequate control causes wrinkles, burns, or uneven shrink.
- 🚫 Neglecting Maintenance: Dirty or malfunctioning tunnels lead to downtime and defective products.
AFM’s Line of Shrink Tunnels
The WSN Series Steam Heat Tunnels for Shrink Sleeve Labeling– The WSN Series Tunnels are designed and manufactured to consistently take on the most difficult shrink labeling operations while keeping energy costs low. Equipped with multiple steam zones and tier adjustable manifolds, WSN tunnels direct the steam heat where needed to produce a precise, high quality finished appearance of PVC, PETG, OPS, and PLA labels and neck bands.
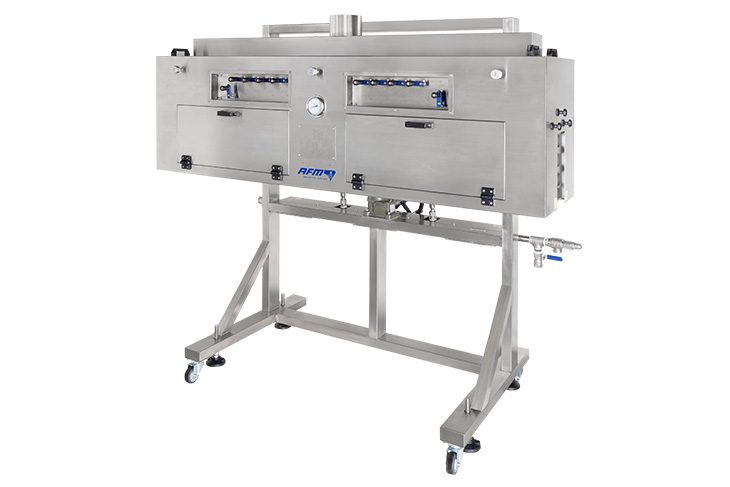
The WSN Series Steam Heat Tunnels for Shrink Sleeve Labeling – The WSN Series Tunnels are designed and manufactured to consistently take on the most difficult shrink labeling operations while keeping energy costs low. Equipped with multiple steam zones and tier adjustable manifolds, WSN tunnels direct the steam heat where needed to produce a precise, high quality finished appearance of PVC, PETG, OPS, and PLA labels and neck bands.
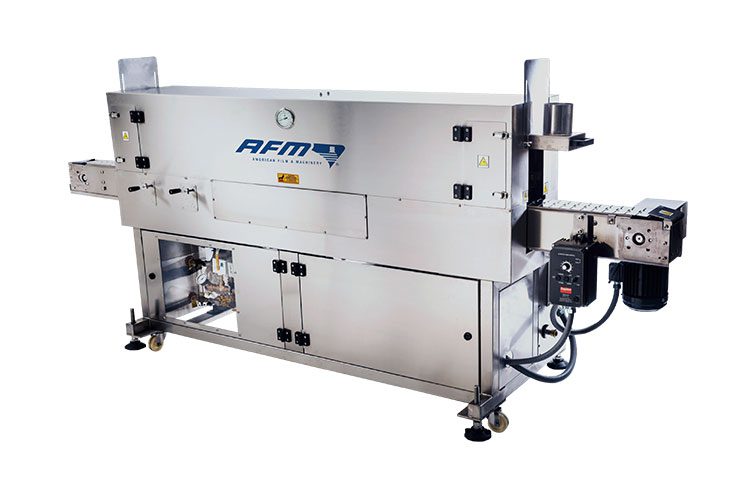
The WSN-GEN S Steam Heat Tunnel for Shrink Sleeve Labeling – The WSN-GEN S is designed for simple setup where in-plant steam generation isn’t readily available. Equipped with 4 adjustable tier manifolds, the GEN S directs the steam heat where needed to produce a precise, high quality finished appearance of PVC, PETG, OPS, PLA labels and
neck bands.
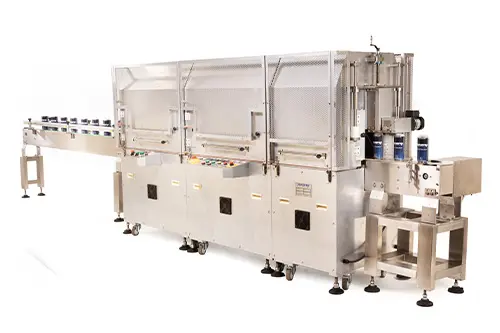
The SRT-2500 Electric Heat Tunnel – AFM’s SRT-2500 is the perfect answer for shrink sleeve labeling applications where steam tunnels are not an option. SRT-2500 utilizes electric heat to provide steam results without using steam. The system comes equipped with three independent shrink zones that allow airflow in each zone to be regulated separately. Zone One is for mild heat and general softening, Zone Two is for more intense overall heat, and Zone Three is for very intense, abrupt heat from all sides for fast and even shrinking. As a result, the SRT-2500 provides optimal shrink control and a high-quality finish on several films including PVC, PET, and OPS.
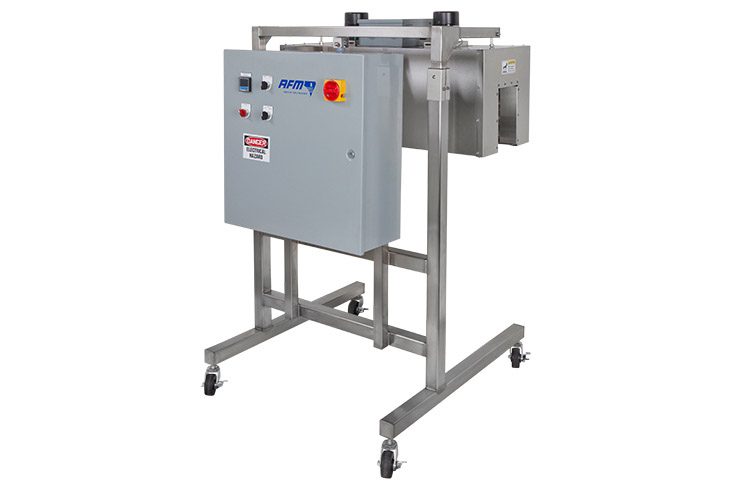
The OAL Classic Radiant Heat Shrink Tunnel for Shrink Sleeve Labeling – The OAL Classic Electric Heat Shrink Tunnel is a versatile and accurate recirculating heat tunnel with high efficiency blowers, adjustable heater element locations, and digital time proportional temperature control with a solid-state contactor. The adjustable IR heater
element locations allow the tunnel to be set up for a wide variety of applications. The OAL Classic provides optimal shrink control and high-quality finish on several films including PVC, PETG, OPS, and PLA.
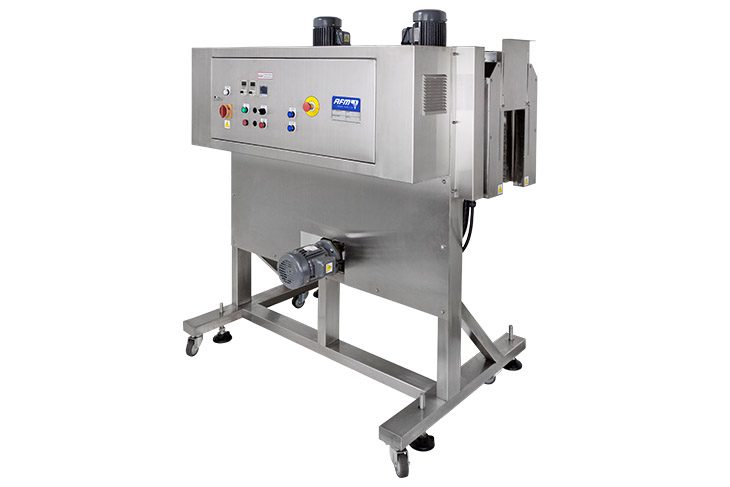
The ES-200 Electric Heat Tunnel for Shrink Sleeve Labeling – The ES-200 Electric Heat Shrink Tunnel comes equipped with two independent VFD air flow controls that allow the air flow in each of the two zones to be regulated separately. The almost infinite air flow adjustment paired with accurate, consistent digital temperature control and adjustable air delivery louvers make the ES-200 an extremely versatile shrink tunnel. The ES-200 provides optimal shrink control and high-quality finish on several films including PVC, PETG, OPS and PLA.
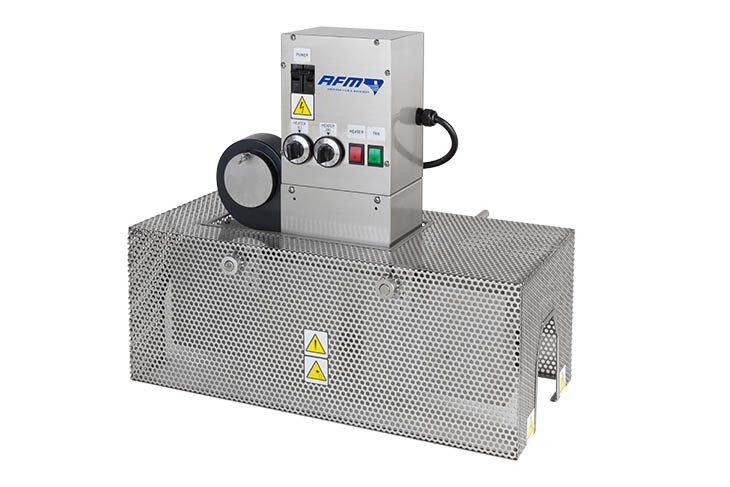
The GS Series Radiant Heat Tunnels for Shrink Sleeve Labeling – GS Series Tunnels are designed to be compact and easy-to-operate additions to your existing shrink band applications. The GS-75 and GS-100 utilize two temperature control regulators for accurate dual heat bank settings and precise band shrinking. Tunnel temperatures are monitored by an external settings control to ensure proper heat distribution across the tunnel chamber, ensuring a high-quality finish on a variety of films including PVC, PETG, OPS, and PLA regardless of container shape.
.
Conclusion: Find the Right Fit for Your Packaging Line
Selecting the right shrink tunnel is more than a purchase — it’s an investment in your production efficiency, product quality, and brand image. By considering your product types, production speeds, film materials, and facility needs, you can choose the equipment that delivers consistent, professional results.
Need help selecting the right shrink tunnel? Our experts at AFM are ready to assist. Contact us today for a consultation, demo, or a quote tailored to your packaging needs.