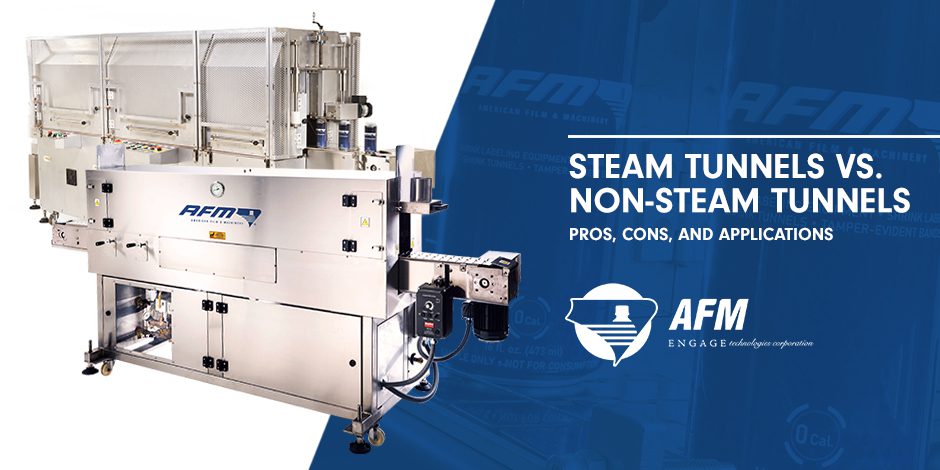
Steam Tunnels vs. Non-Steam Tunnels: Pros, Cons, and Applications
Choosing the right shrink tunnel is essential for achieving the best results for your shrink sleeve labeling and tamper-evident banding operations. Whether you’re working with food and beverage, pharmaceuticals, or consumer goods, your choice of a steam or non-steam heat tunnel can impact both the quality and efficiency of your production line. This blog post compares steam and non-steam heat tunnels, highlighting their pros, cons, and ideal applications. Read on to find the right shrink tunnel for your needs.
Steam Heat Tunnels: How They Work
Steam heat tunnels use the power of steam to evenly apply heat to shrinkable materials, ensuring a smooth, consistent shrink around containers. Steam heat tunnels are especially effective for handling complex container shapes and various shrink films like PVC, PETG, OPS, and PLA. The WSN Series Steam Heat Tunnels and WSN-GEN S from American Film & Machinery (AFM) are examples of highly efficient steam tunnels designed to meet diverse shrink labeling needs.
The WSN Series is equipped with multiple steam zones, allowing for precise heat application, even for full body and cap shrink applications. These tunnels are perfect for industries such as food & beverage, pharmaceuticals, and cosmetics. For situations where in-plant steam is unavailable, the WSN-GEN S includes a built-in steam generator, making it an excellent choice for facilities without existing steam infrastructure.
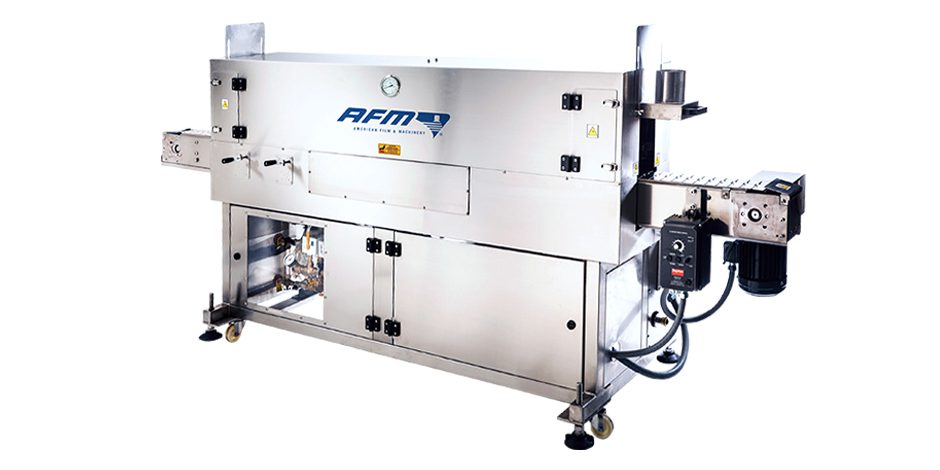
Pros and Cons of Steam Heat Tunnels
Pros:
- Uniform Shrink: Steam tunnels provide consistent, high-quality shrink results, ensuring smooth, professional-looking labels.
- Precision: With adjustable steam zones, steam tunnels allow for precise heat application, making them ideal for a variety of container shapes and sizes.
- Versatile Applications: These tunnels are suitable for numerous industries, including food and beverage, pharmaceuticals, and consumer goods.
Cons:
- Infrastructure: Steam tunnels require a reliable steam source, which can lead to additional infrastructure and maintenance costs. The need for a boiler and regular maintenance can be a downside for some operations.
- Moisture Sensitivity: Steam heat tunnels are not suitable for moisture-sensitive products as they expose containers to steam, which can damage certain materials.
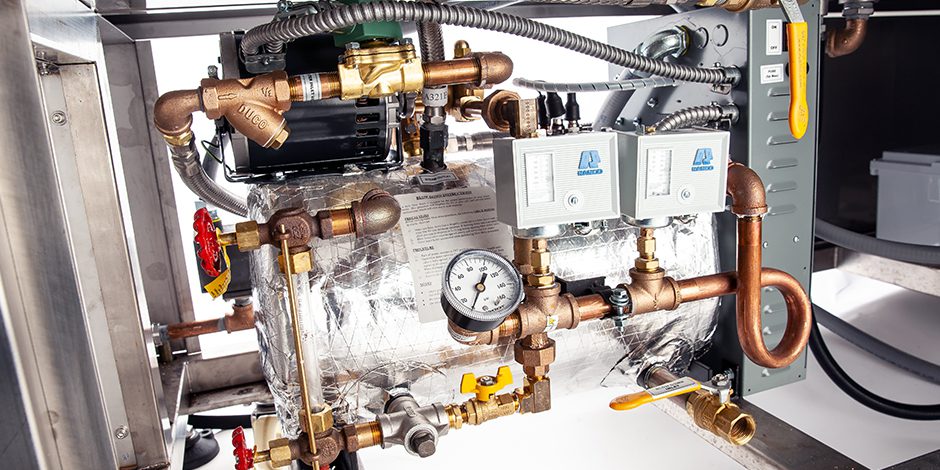
Non-Steam Heat Tunnels: How They Work
Non-steam heat tunnels, such as the SRT-2500 Electric Heat Tunnel, GS Series Radiant Heat Tunnels, and OAL Classic Radiant Heat Tunnel, use electric and radiant heat to shrink labels. These systems are ideal for applications where steam is either impractical or undesirable. Non-steam heat tunnels are particularly effective for sleeving powdered products, empty containers, or products sensitive to moisture exposure.
The SRT-2500 electric heat tunnel provides uniform shrink results without the need for steam, making it perfect for products where moisture is a concern. The GS Series Radiant Heat Tunnels and OAL Classic utilize high-efficiency blowers and adjustable heater elements to provide precision shrink results, especially in smaller applications or where quick changeovers are required.
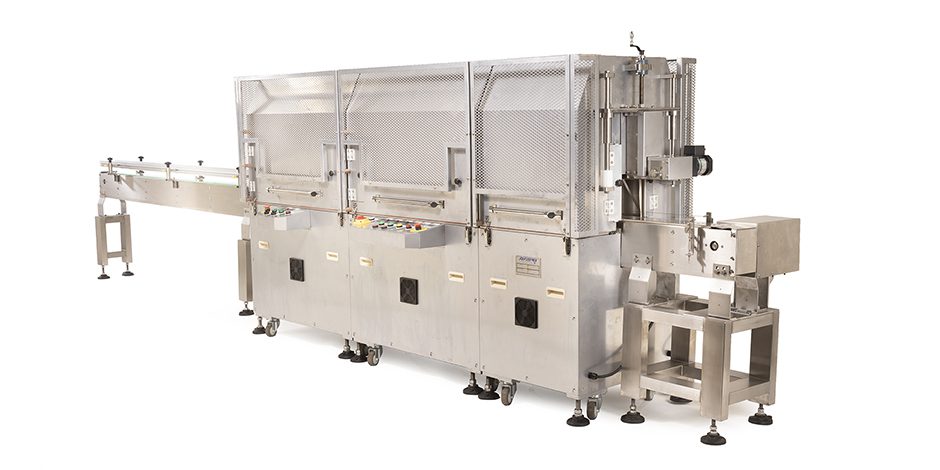
Pros:
- No Steam Infrastructure: Non-steam tunnels eliminate the need for a boiler and reduce operational costs associated with steam production.
- Ideal for Moisture-Sensitive Products: These tunnels are perfect for powdered products, empty containers, or products that cannot tolerate moisture.
- Easy Operation: Non-steam tunnels, such as the OAL Classic, feature adjustable heater locations and simple control interfaces, making them easy to set up and maintain.
- Flexibility: These systems are ideal for contract packagers and operations with varying production requirements.
Cons:
- Less Uniform Shrink: Non-steam heat tunnels may not provide the same level of uniform shrink as steam tunnels. Achieving optimal results may require more precise adjustments.
- Limited Effectiveness on Complex Shapes: While effective for simpler products, non-steam tunnels may struggle with irregular or intricate container shapes compared to steam heat tunnels.
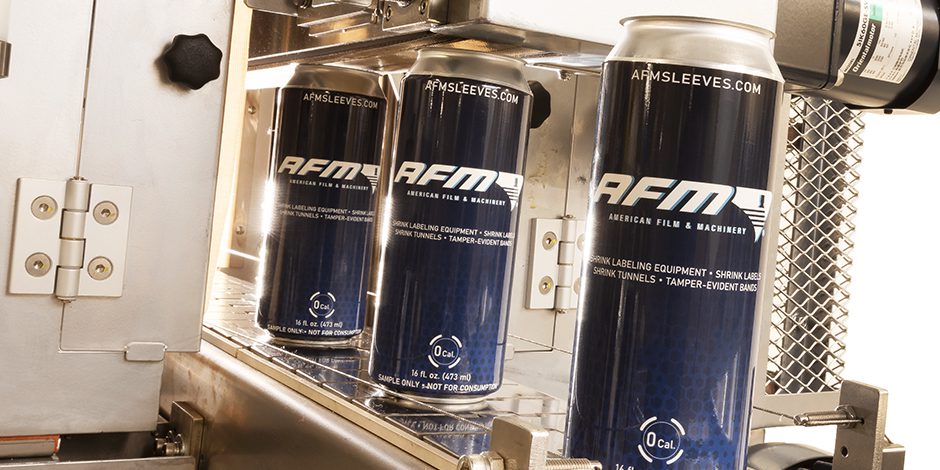
Choosing the Right Tunnel for Your Application
The decision between steam and non-steam heat tunnels depends on several factors, including product type, container material, and production environment. Steam heat tunnels are best suited for operations where a consistent, uniform shrink is crucial, and the product can withstand exposure to moisture. In contrast, non-steam heat tunnels are ideal for products that cannot be exposed to steam or where cost efficiency and ease of operation are priorities.
For industries like food and beverage, pharmaceuticals, and consumer goods, steam heat tunnels often provide the most reliable results. However, for businesses dealing with moisture-sensitive products or looking for a more flexible, lower-maintenance solution, non-steam heat tunnels can be a better choice.
Conclusion
Both steam and non-steam heat tunnels have their place in the world of shrink sleeve labeling. By considering your specific production needs and product requirements, you can select the best solution for your operation. Contact AFM to learn more about which heat tunnel system would best suit your needs and help you achieve the highest quality shrink labeling results.